Amorphous Coils and Core for Transformers
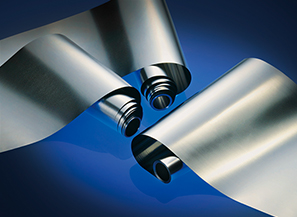
Amorphous metal is an alloy with a non crystalline structure produced by ultra-rapid quenching (about 1 million ℃ per second) of molten alloy. Because amorphous metal has no anisotropic properties, which originated from a crystalline structure, and there are no crystalline grain boundaries to prevent motion of magnetic domain walls, it shows excellent magnetic properties such as high permeability and low loss while having a high-saturation magnetic flux density. Amorphous metal materials for transformers, whose main ingredient is Fe (iron), are used in power line transformers and industrial transformers. Compared to conventional materials such as silicon steel, amorphous metal materials have a small no-load loss (iron loss), 1/5 that of silicon steel. Therefore, they make a major contribution to energy conservation. Proterial provides amorphous metal ribbon.
More than ever, electric utilities and industries today are searching for technologies that will reduce their operating costs and improve energy savings throughout their systems. New transmission and distribution (T&D) technologies are now available to help utilities meet these goals.
With Proterial amorphous metal distribution transformers
(AMDTs) — with up to 70% lower core loss than
conventional transformers — Proterial is helping utilities
worldwide to achieve their efficiency objectives. When you
consider that 15 % of all electricity generated by
utilities is lost in the transmission & distribution
process, the potential savings through reductions in core
loss can be significant.
Ultra-efficient transformer cores made with Proterial’s
amorphous metal alloy make lower core losses possible.
Amorphous metal distribution transformers are key to
improving utility economics and enhancing energy
conservation efforts worldwide.
There are two grades of amorphous Ribbon available with us
- 1. 605HB1M
- 2. 2605SA1
Please submit your enquiry for requesting a quote.
HIGH PERFORMANCE BRAZING FILLER METALS
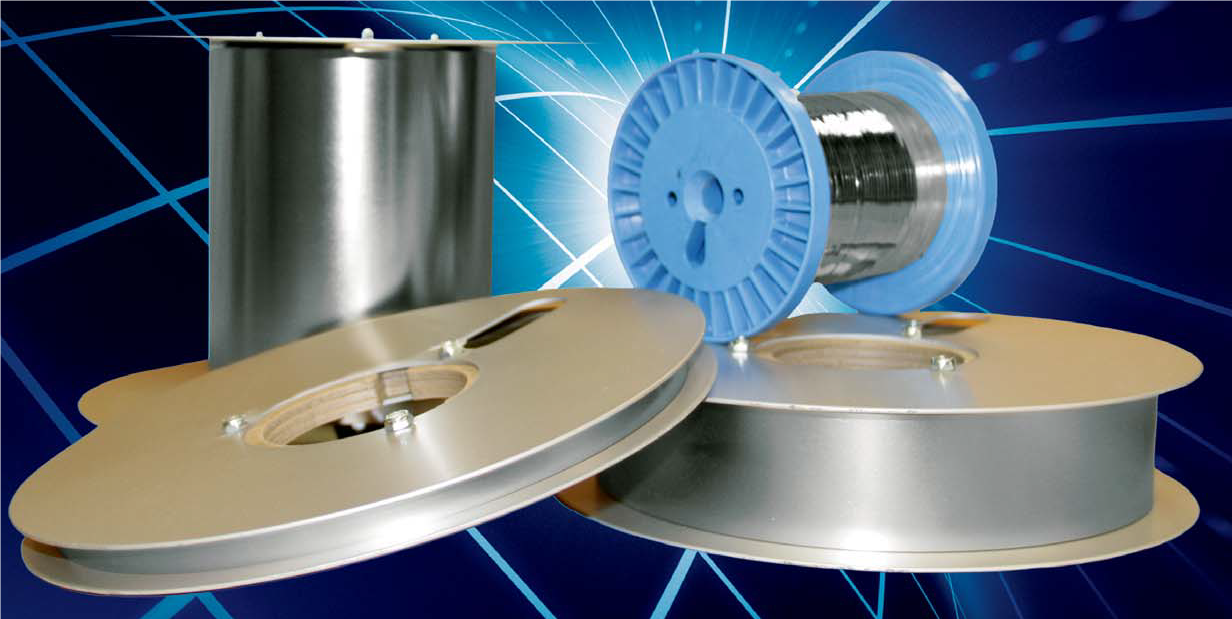
Brazing Foils and preforms provide extensive manufacturing and performance advantages over conventional metal joining materials. This unique form of amorphous nickel based brazing filler metal can substitute for previously used copper foil or nickel powder to braze stainless steel base metal. This amorphous nickel foil provides high strength and outstanding corrosion resistance of brazed joints.
APPLICATIONS FOR BRAZING FOIL
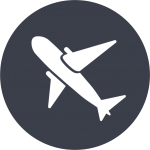
Aerospace
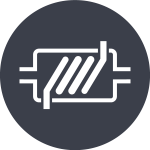
Heat Exchangers
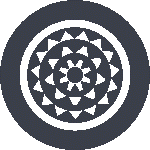
Substrates
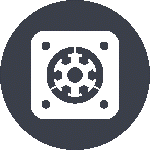
Preforms
Advantages over Powder/Pastes/Tapes
Metglas® Brazing Foil
- Ductile, Flexible, 100% Metallic Foil.
- Melts Quickly within a Narrow Temperature Range.
- Creates Strong and void-free Joints.
- Can Be Placed with Precision Between Parts.
- Very Economical and Effective Vs. Powder Metal Fillers.
- Reduces Set Up and Assembly Process Time.
- Does not Harm the Environment or Vacuum Brazing Furnaces.
Conventional Brazing Fillers.
- Generally Brittle Powders.
- Melts Slower than MBF with Wider Temperature Range.
- Excessive Amount of Detrimental Oxides.
- Larger Quantities Required per Joint than MBF.
- Prone to Form Porous Joints with Large Crystalline Grains.
- Messy and Difficult Assembly Processing.
- Contaminates the Environment and Degrades Vacuum
Brazing Furnaces.